La tecnologia LPF (Low Pressure Forging) combina i vantaggi del riempimento in bassa pressione con un’azione di forgiatura, producendo componenti in leghe di alluminio dalle eccellenti proprietà meccaniche e prodotti con tempi ciclo molto minori rispetto alle analoghe tecnologie concorrenti.
LPF
(Low Pressure Forging)
L’evoluzione della fusione e forgiatura
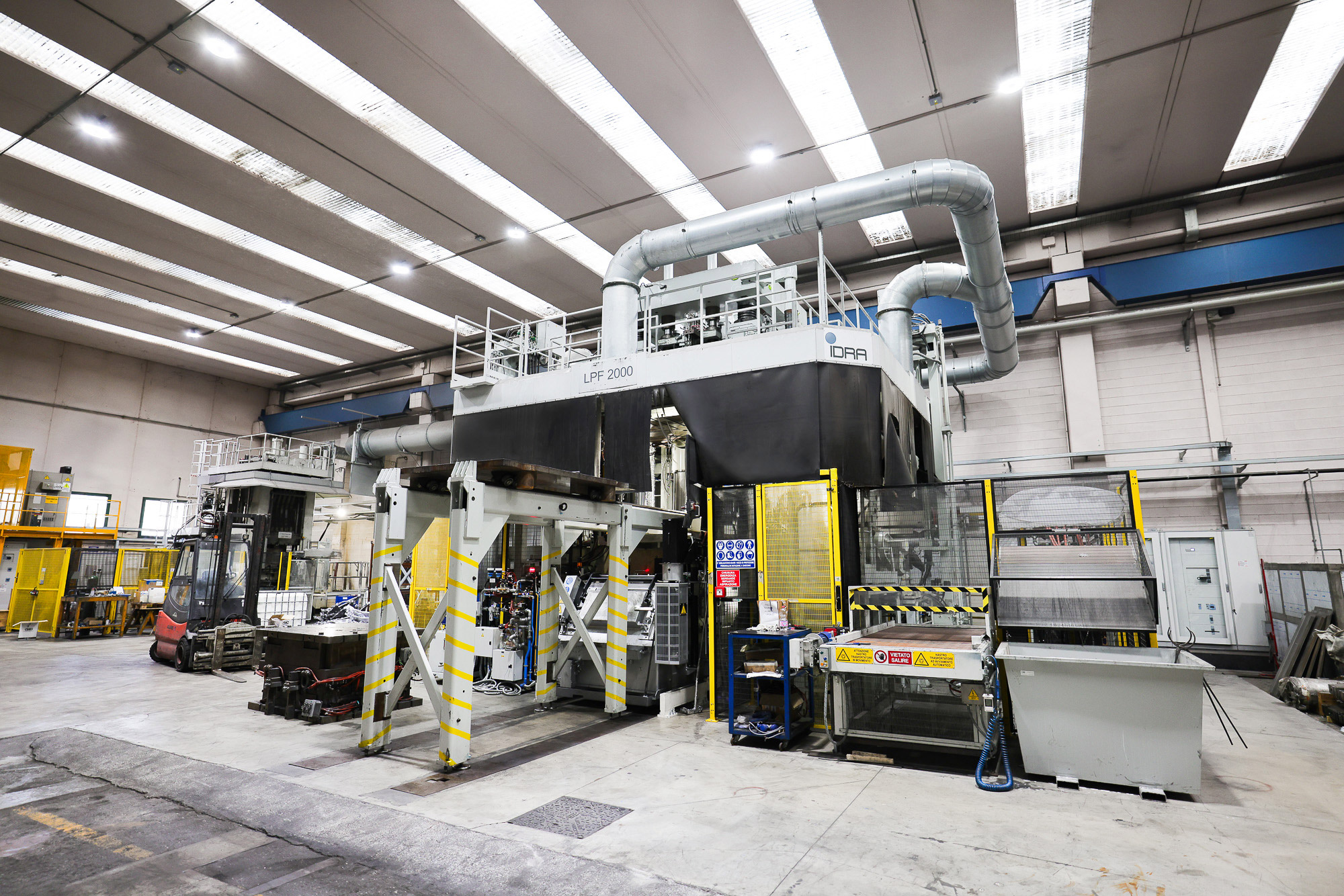
Vantaggi principali della tecnologia LPF
-
Riduzione dei tempi di ciclo
Rispetto alla tecnologia Low Pressure tradizionale, LPF permette di ottenere cicli produttivi enormemente più rapidi.
-
Proprietà meccaniche superiori
I componenti prodotti con tecnologia LPF presentano proprietà meccaniche comparabili a quelle ottenute tramite forgiatura tradizionale.
-
Leghe speciali
Consente l’uso di leghe di alluminio a basso contenuto di silicio, difficili da utilizzare con altre tecniche di fusione.
-
Flessibilità progettuale
LPF offre maggiore libertà di progettazione della geometria del prodotto (rispetto al forgiato) e una migliore precisione dimensionale (rispetto alla LPDC).
-
Riduzione dei tempi di ciclo
Rispetto alla tecnologia Low Pressure tradizionale, LPF permette di ottenere cicli produttivi enormemente più rapidi.
-
Proprietà meccaniche superiori
I componenti prodotti con tecnologia LPF presentano proprietà meccaniche comparabili a quelle ottenute tramite forgiatura tradizionale.
-
Leghe speciali
Consente l’uso di leghe di alluminio a basso contenuto di silicio, difficili da utilizzare con altre tecniche di fusione.
-
Flessibilità progettuale
LPF offre maggiore libertà di progettazione della geometria del prodotto (rispetto al forgiato) e una migliore precisione dimensionale (rispetto alla LPDC).
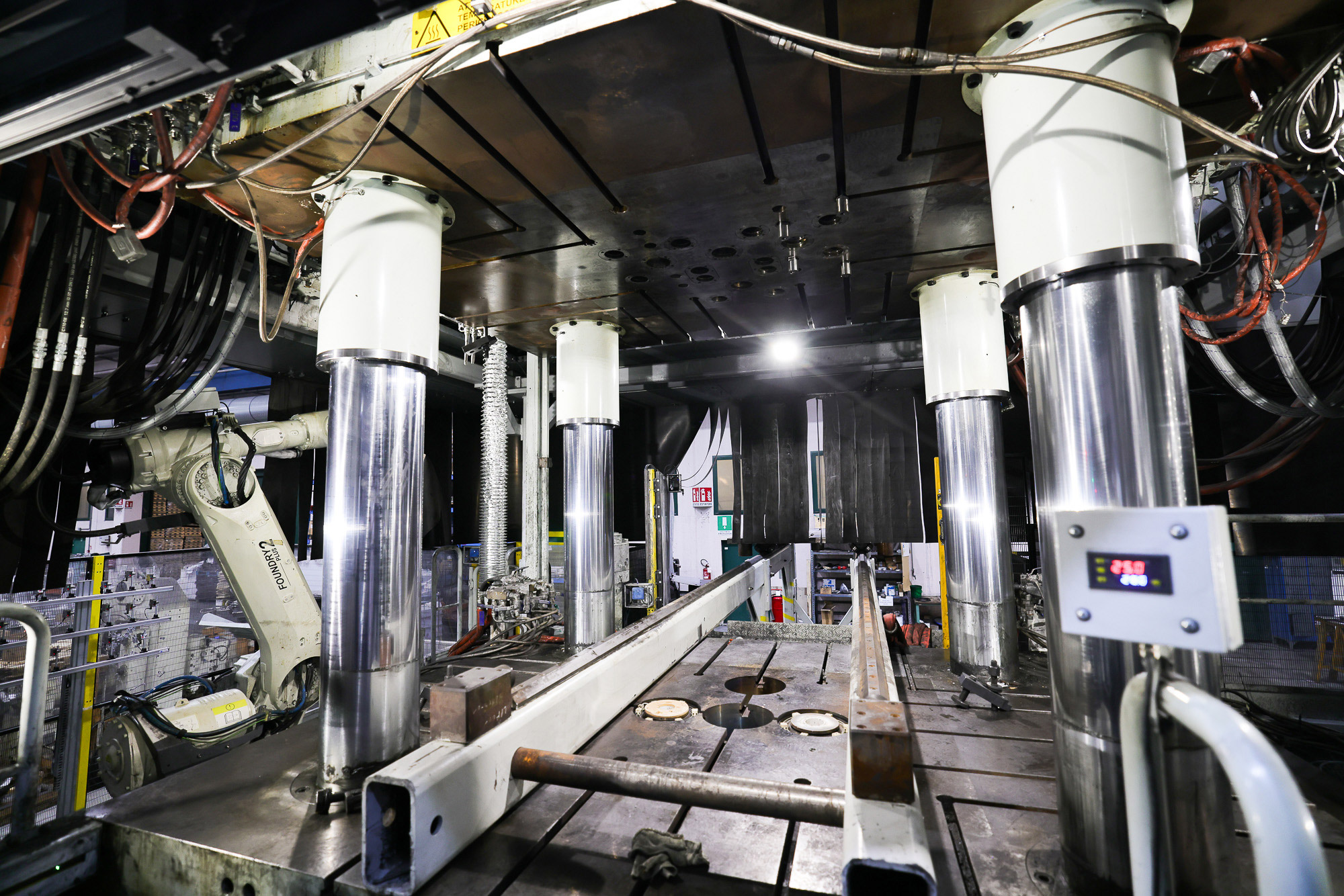
L'innovazione nel campo della fusione e forgiatura.
Le principali applicazioni della tecnologia LPF includono ad esempio componenti strutturali per il settore automotive, bracci e snodi sospensione, pinze per freni e ruote. La produzione di questi componenti con tecnologia LPF rappresenta un’opzione vantaggiosa rispetto alla forgiatura a caldo per i costi ridotti e rispetto alla LPDC per prestazioni meccaniche superiori.
In collaborazione con Idra, fornitore leader di macchinari per la fusione, abbiamo installato nel 2020 una pressa sperimentale da 600 tonnellate, seguita da una pressa da 2000 tonnellate per test e produzione di serie.