The LPF (Low Pressure Forging) technology combines the benefits of low-pressure filling with a forging action, producing aluminum alloy components with excellent mechanical properties and significantly shorter cycle times compared to competing technologies.
LPF
(Low Pressure Forging)
The evolution of casting and forging
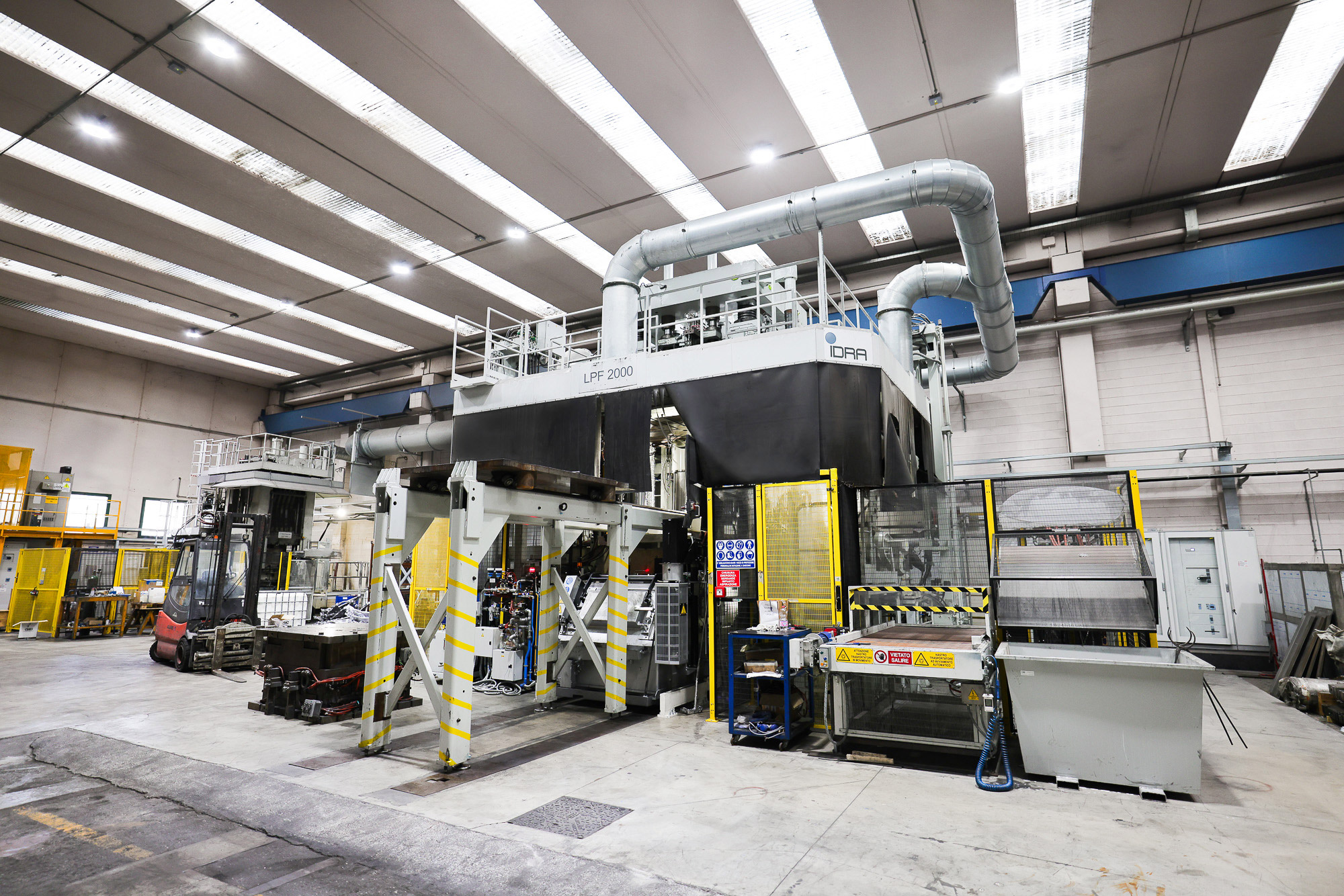
Key advantages of LPF technology
-
Reduced cycle times
Compared to traditional Low-Pressure technology, LPF enables significantly faster production cycles.
-
Superior mechanical properties
Components produced using LPF technology exhibit mechanical properties comparable to those achieved through traditional forging.
-
Special alloys
Allows the use of low-silicon aluminum alloys, which are difficult to process with other casting techniques.
-
Design flexibility
LPF provides greater freedom in product geometry design (compared to forging) and improved dimensional precision (compared to LPDC).
-
Reduced cycle times
Compared to traditional Low-Pressure technology, LPF enables significantly faster production cycles.
-
Superior mechanical properties
Components produced using LPF technology exhibit mechanical properties comparable to those achieved through traditional forging.
-
Special alloys
Allows the use of low-silicon aluminum alloys, which are difficult to process with other casting techniques.
-
Design flexibility
LPF provides greater freedom in product geometry design (compared to forging) and improved dimensional precision (compared to LPDC).
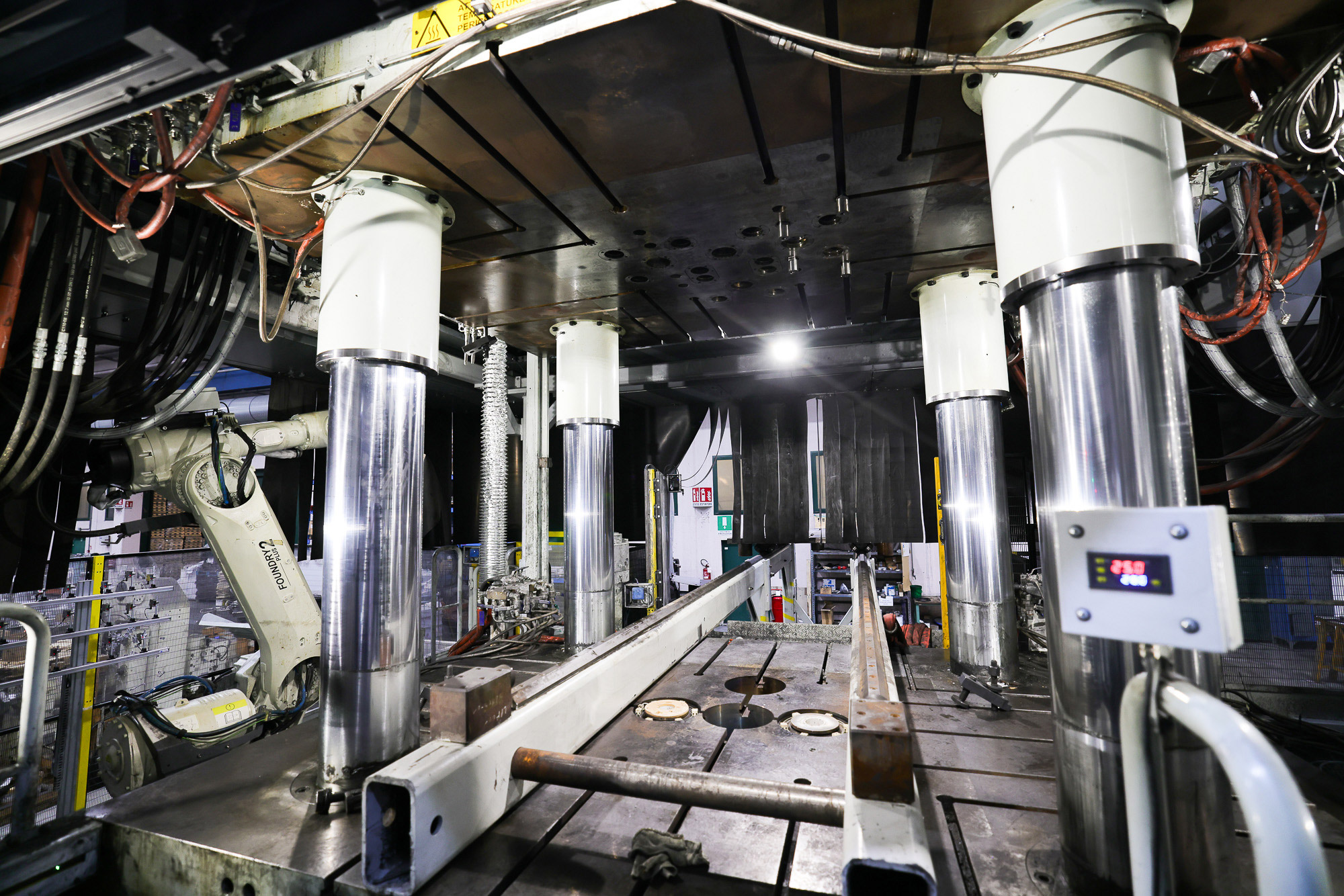
Innovation in casting and forging.
Major applications of LPF technology include, for example, automotive structural components, suspension arms and joints, brake calipers and wheels. Manufacturing these components with LPF technology is an advantageous option over hot forging for reduced cost and over LPDC for superior mechanical performance.
In collaboration with Idra, a leading supplier of casting machinery, we installed an experimental 600-ton press in 2020, followed by a 2000-ton press for testing and mass production.